हाल के वर्षों में, नए ऊर्जा उद्योग के तेजी से विकास के कारण, लेजर वेल्डिंग ने अपने तेज और स्थिर लाभों के कारण पूरे नए ऊर्जा उद्योग में तेजी से प्रवेश किया है। उनमें से, लेजर वेल्डिंग उपकरण पूरे नए ऊर्जा उद्योग में अनुप्रयोगों के उच्चतम अनुपात के लिए जिम्मेदार है।
लेसर वेल्डिंगअपनी तेज गति, बड़ी गहराई और छोटी विकृति के कारण यह जीवन के सभी क्षेत्रों में पहली पसंद बन गया है। स्पॉट वेल्ड से लेकर बट वेल्ड, बिल्ड-अप और सील वेल्ड तक,लेसर वेल्डिंगअद्वितीय सटीकता और नियंत्रण प्रदान करता है। यह सैन्य उद्योग, चिकित्सा देखभाल, एयरोस्पेस, 3सी ऑटो पार्ट्स, मैकेनिकल शीट मेटल, नई ऊर्जा और अन्य उद्योगों सहित औद्योगिक उत्पादन और विनिर्माण में महत्वपूर्ण भूमिका निभाता है।
अन्य वेल्डिंग प्रौद्योगिकियों की तुलना में, लेजर वेल्डिंग के अपने अद्वितीय फायदे और नुकसान हैं।
फ़ायदा:
1. तेज गति, बड़ी गहराई और छोटी विकृति।
2. वेल्डिंग सामान्य तापमान पर या विशेष परिस्थितियों में की जा सकती है, और वेल्डिंग उपकरण सरल है। उदाहरण के लिए, एक लेजर किरण विद्युत चुम्बकीय क्षेत्र में बहती नहीं है। लेजर निर्वात, वायु या कुछ गैस वातावरण में वेल्ड कर सकते हैं, और कांच के माध्यम से या लेजर बीम के लिए पारदर्शी सामग्री को वेल्ड कर सकते हैं।
3. यह टाइटेनियम और क्वार्ट्ज जैसी दुर्दम्य सामग्रियों को वेल्ड कर सकता है, और अच्छे परिणामों के साथ असमान सामग्रियों को भी वेल्ड कर सकता है।
4. लेज़र पर ध्यान केंद्रित करने के बाद, शक्ति घनत्व अधिक होता है। उच्च-शक्ति उपकरणों को वेल्डिंग करते समय पहलू अनुपात 5:1 तक पहुंच सकता है, और 10:1 तक पहुंच सकता है।
5. माइक्रो वेल्डिंग की जा सकती है। लेज़र बीम पर ध्यान केंद्रित करने के बाद, एक छोटा सा स्थान प्राप्त किया जा सकता है और उसे सटीक रूप से स्थित किया जा सकता है। इसे स्वचालित बड़े पैमाने पर उत्पादन प्राप्त करने के लिए सूक्ष्म और छोटे वर्कपीस की असेंबली और वेल्डिंग पर लागू किया जा सकता है।
6. यह दुर्गम क्षेत्रों को वेल्ड कर सकता है और बड़े लचीलेपन के साथ गैर-संपर्क लंबी दूरी की वेल्डिंग कर सकता है। विशेष रूप से हाल के वर्षों में, YAG लेजर प्रसंस्करण प्रौद्योगिकी ने ऑप्टिकल फाइबर ट्रांसमिशन तकनीक को अपनाया है, जिसने लेजर वेल्डिंग तकनीक को अधिक व्यापक रूप से बढ़ावा देने और लागू करने में सक्षम बनाया है।
7. लेजर बीम को समय और स्थान में विभाजित करना आसान है, और कई बीमों को एक साथ कई स्थानों पर संसाधित किया जा सकता है, जो अधिक सटीक वेल्डिंग के लिए स्थितियां प्रदान करता है।
दोष:
1. वर्कपीस की असेंबली सटीकता अधिक होनी आवश्यक है, और वर्कपीस पर बीम की स्थिति को महत्वपूर्ण रूप से विचलित नहीं किया जा सकता है। ऐसा इसलिए है क्योंकि फोकस करने के बाद लेजर स्पॉट का आकार छोटा होता है और वेल्ड सीम संकीर्ण होता है, जिससे फिलर धातु सामग्री जोड़ना मुश्किल हो जाता है। यदि वर्कपीस की असेंबली सटीकता या बीम की स्थिति सटीकता आवश्यकताओं को पूरा नहीं करती है, तो वेल्डिंग दोष उत्पन्न होने का खतरा होता है।
2. लेजर और संबंधित प्रणालियों की लागत अधिक है, और एकमुश्त निवेश बड़ा है।
सामान्य लेजर वेल्डिंग दोषलिथियम बैटरी निर्माण में
1. वेल्डिंग सरंध्रता
में सामान्य दोषलेसर वेल्डिंगछिद्र हैं. वेल्डिंग पिघला हुआ पूल गहरा और संकीर्ण है। लेजर वेल्डिंग प्रक्रिया के दौरान, नाइट्रोजन बाहर से पिघले हुए पूल पर आक्रमण करती है। धातु के ठंडा होने और जमने की प्रक्रिया के दौरान, तापमान घटने के साथ नाइट्रोजन की घुलनशीलता कम हो जाती है। जब पिघली हुई पूल धातु ठंडी होकर क्रिस्टलीकृत होने लगती है, तो घुलनशीलता तेजी से और अचानक कम हो जाएगी। इस समय, बड़ी मात्रा में गैस अवक्षेपित होकर बुलबुले बनाएगी। यदि बुलबुले की तैरने की गति धातु के क्रिस्टलीकरण की गति से कम है, तो छिद्र उत्पन्न होंगे।
लिथियम बैटरी उद्योग में अनुप्रयोगों में, हम अक्सर पाते हैं कि सकारात्मक इलेक्ट्रोड की वेल्डिंग के दौरान छिद्र विशेष रूप से होने की संभावना होती है, लेकिन नकारात्मक इलेक्ट्रोड की वेल्डिंग के दौरान शायद ही कभी होते हैं। ऐसा इसलिए है क्योंकि सकारात्मक इलेक्ट्रोड एल्यूमीनियम से बना है और नकारात्मक इलेक्ट्रोड तांबे से बना है। वेल्डिंग के दौरान, आंतरिक गैस के पूरी तरह से ओवरफ्लो होने से पहले सतह पर तरल एल्यूमीनियम संघनित हो जाता है, जिससे गैस को ओवरफ्लो होने और बड़े और छोटे छेद बनने से रोका जाता है। छोटे रंध्र.
ऊपर वर्णित छिद्रों के कारणों के अलावा, छिद्रों में बाहरी हवा, नमी, सतह का तेल आदि भी शामिल हैं। इसके अलावा, नाइट्रोजन बहने की दिशा और कोण भी छिद्रों के निर्माण को प्रभावित करेंगे।
वेल्डिंग छिद्रों की घटना को कैसे कम करें?
पहले, पहलेवेल्डिंग, आने वाली सामग्रियों की सतह पर तेल के दाग और अशुद्धियों को समय पर साफ करने की आवश्यकता है; लिथियम बैटरी के उत्पादन में, आने वाली सामग्री का निरीक्षण एक आवश्यक प्रक्रिया है।
दूसरा, परिरक्षण गैस प्रवाह को वेल्डिंग गति, शक्ति, स्थिति इत्यादि जैसे कारकों के अनुसार समायोजित किया जाना चाहिए, और न तो बहुत बड़ा होना चाहिए और न ही बहुत छोटा होना चाहिए। सुरक्षात्मक लबादा दबाव को लेजर शक्ति और फोकस स्थिति जैसे कारकों के अनुसार समायोजित किया जाना चाहिए, और न तो बहुत अधिक और न ही बहुत कम होना चाहिए। सुरक्षात्मक लबादा नोजल के आकार को वेल्ड के आकार, दिशा और अन्य कारकों के अनुसार समायोजित किया जाना चाहिए ताकि सुरक्षात्मक लबादा वेल्डिंग क्षेत्र को समान रूप से कवर कर सके।
तीसरा, कार्यशाला में हवा में तापमान, आर्द्रता और धूल को नियंत्रित करें। परिवेश का तापमान और आर्द्रता सब्सट्रेट और सुरक्षात्मक गैस की सतह पर नमी की मात्रा को प्रभावित करेगी, जो बदले में पिघले हुए पूल में जल वाष्प के उत्पादन और निकास को प्रभावित करेगी। यदि परिवेश का तापमान और आर्द्रता बहुत अधिक है, तो सब्सट्रेट और सुरक्षात्मक गैस की सतह पर बहुत अधिक नमी होगी, जिससे बड़ी मात्रा में जल वाष्प उत्पन्न होगा, जिसके परिणामस्वरूप छिद्र होंगे। यदि परिवेश का तापमान और आर्द्रता बहुत कम है, तो सब्सट्रेट की सतह और परिरक्षण गैस में बहुत कम नमी होगी, जिससे जल वाष्प का उत्पादन कम हो जाएगा, जिससे छिद्र कम हो जाएंगे; गुणवत्ता कर्मियों को वेल्डिंग स्टेशन पर तापमान, आर्द्रता और धूल के लक्ष्य मूल्य का पता लगाने दें।
चौथा, बीम स्विंग विधि का उपयोग लेजर डीप पेनेट्रेशन वेल्डिंग में छिद्रों को कम करने या खत्म करने के लिए किया जाता है। वेल्डिंग के दौरान स्विंग के जुड़ने के कारण, वेल्ड सीम के लिए बीम के प्रत्यागामी स्विंग के कारण वेल्ड सीम का हिस्सा बार-बार पिघलता है, जो वेल्डिंग पूल में तरल धातु के निवास समय को बढ़ाता है। साथ ही, बीम के विक्षेपण से प्रति इकाई क्षेत्र में ऊष्मा इनपुट भी बढ़ जाता है। वेल्ड की गहराई-से-चौड़ाई का अनुपात कम हो जाता है, जो बुलबुले के उद्भव के लिए अनुकूल है, जिससे छिद्र समाप्त हो जाते हैं। दूसरी ओर, बीम का स्विंग छोटे छेद को तदनुसार स्विंग करने का कारण बनता है, जो वेल्डिंग पूल के लिए एक सरगर्मी बल भी प्रदान कर सकता है, वेल्डिंग पूल के संवहन और सरगर्मी को बढ़ा सकता है, और छिद्रों को खत्म करने पर लाभकारी प्रभाव डाल सकता है।
पांचवां, पल्स आवृत्ति, पल्स आवृत्ति प्रति यूनिट समय में लेजर बीम द्वारा उत्सर्जित दालों की संख्या को संदर्भित करती है, जो पिघले हुए पूल में गर्मी इनपुट और गर्मी संचय को प्रभावित करेगी, और फिर पिघले हुए पूल में तापमान क्षेत्र और प्रवाह क्षेत्र को प्रभावित करेगी। पूल। यदि पल्स आवृत्ति बहुत अधिक है, तो इससे पिघले हुए पूल में अत्यधिक ताप इनपुट हो जाएगा, जिससे पिघले हुए पूल का तापमान बहुत अधिक हो जाएगा, जिससे धातु वाष्प या अन्य तत्व उत्पन्न होंगे जो उच्च तापमान पर अस्थिर होते हैं, जिसके परिणामस्वरूप छिद्र हो जाते हैं। यदि पल्स आवृत्ति बहुत कम है, तो इससे पिघले हुए पूल में अपर्याप्त गर्मी संचय हो जाएगा, जिससे पिघले हुए पूल का तापमान बहुत कम हो जाएगा, जिससे गैस का विघटन और निकास कम हो जाएगा, जिसके परिणामस्वरूप छिद्र हो जाएंगे। सामान्यतया, पल्स आवृत्ति को सब्सट्रेट की मोटाई और लेजर शक्ति के आधार पर उचित सीमा के भीतर चुना जाना चाहिए, और बहुत अधिक या बहुत कम होने से बचना चाहिए।
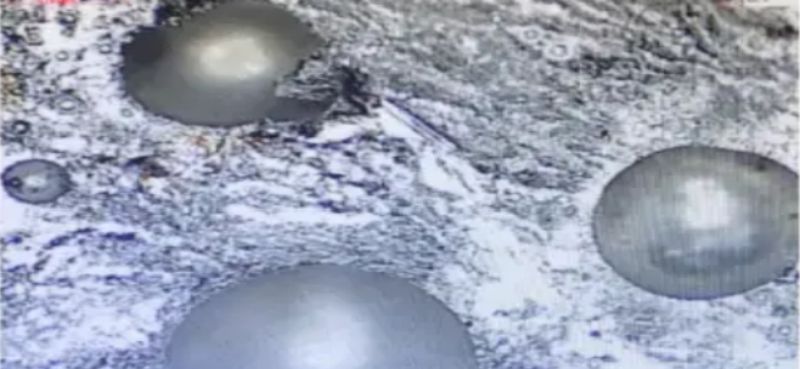
वेल्डिंग छेद (लेजर वेल्डिंग)
2. वेल्ड स्पैटर
वेल्डिंग प्रक्रिया, लेजर वेल्डिंग के दौरान उत्पन्न छींटे वेल्ड की सतह की गुणवत्ता को गंभीर रूप से प्रभावित करेंगे, और लेंस को प्रदूषित और क्षतिग्रस्त कर देंगे। सामान्य प्रदर्शन इस प्रकार है: लेजर वेल्डिंग पूरा होने के बाद, कई धातु कण सामग्री या वर्कपीस की सतह पर दिखाई देते हैं और सामग्री या वर्कपीस की सतह से चिपक जाते हैं। सबसे सहज प्रदर्शन यह है कि गैल्वेनोमीटर के मोड में वेल्डिंग करते समय, गैल्वेनोमीटर के सुरक्षात्मक लेंस के उपयोग की अवधि के बाद, सतह पर घने गड्ढे होंगे, और ये गड्ढे वेल्डिंग स्पैटर के कारण होते हैं। लंबे समय के बाद, प्रकाश को अवरुद्ध करना आसान होता है, और वेल्डिंग प्रकाश के साथ समस्याएं होंगी, जिसके परिणामस्वरूप टूटी हुई वेल्डिंग और आभासी वेल्डिंग जैसी समस्याओं की एक श्रृंखला होगी।
छींटे पड़ने के कारण क्या हैं?
सबसे पहले, बिजली घनत्व, बिजली घनत्व जितना अधिक होगा, स्पैटर उत्पन्न करना उतना ही आसान होगा, और स्पैटर सीधे बिजली घनत्व से संबंधित है। यह एक सदी पुरानी समस्या है. कम से कम अब तक, उद्योग छींटों की समस्या को हल करने में असमर्थ रहा है, और केवल यह कह सकता है कि इसे थोड़ा कम कर दिया गया है। लिथियम बैटरी उद्योग में, छींटे बैटरी शॉर्ट सर्किट का सबसे बड़ा दोषी है, लेकिन यह मूल कारण को हल करने में सक्षम नहीं है। सुरक्षा की दृष्टि से ही बैटरी पर छींटों के प्रभाव को कम किया जा सकता है। उदाहरण के लिए, वेल्डिंग भाग के चारों ओर धूल हटाने वाले बंदरगाहों और सुरक्षात्मक आवरणों का एक चक्र जोड़ा जाता है, और छींटों के प्रभाव या यहां तक कि बैटरी को नुकसान से बचाने के लिए वायु चाकू की पंक्तियों को हलकों में जोड़ा जाता है। वेल्डिंग स्टेशन के आसपास के पर्यावरण, उत्पादों और घटकों को नष्ट करने के बारे में कहा जा सकता है कि साधन समाप्त हो गए हैं।
जहाँ तक छींटे की समस्या को हल करने की बात है, तो केवल यही कहा जा सकता है कि वेल्डिंग ऊर्जा को कम करने से छींटे को कम करने में मदद मिलती है। यदि पैठ अपर्याप्त है तो वेल्डिंग गति को कम करने से भी मदद मिल सकती है। लेकिन कुछ विशेष प्रक्रिया आवश्यकताओं में इसका प्रभाव बहुत कम होता है। यह एक ही प्रक्रिया है, विभिन्न मशीनों और सामग्रियों के विभिन्न बैचों में पूरी तरह से अलग-अलग वेल्डिंग प्रभाव होते हैं। इसलिए, नई ऊर्जा उद्योग में एक अलिखित नियम है, उपकरण के एक टुकड़े के लिए वेल्डिंग मापदंडों का एक सेट।
दूसरा, यदि संसाधित सामग्री या वर्कपीस की सतह को साफ नहीं किया जाता है, तो तेल के दाग या प्रदूषक भी गंभीर छींटों का कारण बनेंगे। इस समय, सबसे आसान काम संसाधित सामग्री की सतह को साफ करना है।
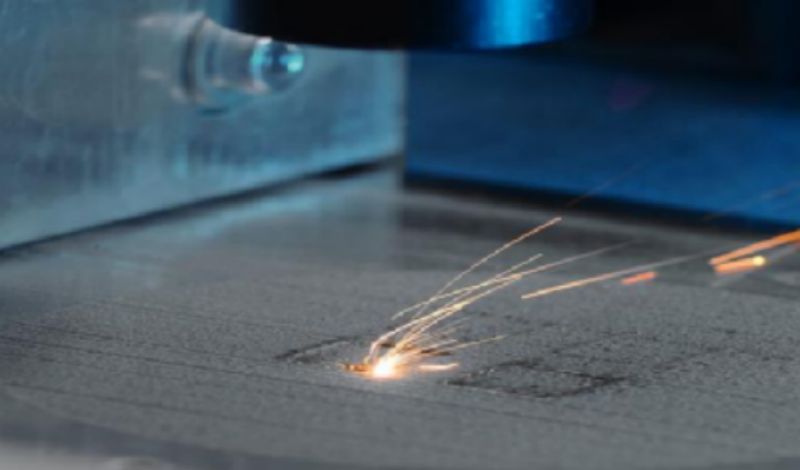
3. लेजर वेल्डिंग की उच्च परावर्तनशीलता
आम तौर पर, उच्च प्रतिबिंब इस तथ्य को संदर्भित करता है कि प्रसंस्करण सामग्री में कम प्रतिरोधकता, अपेक्षाकृत चिकनी सतह और निकट-अवरक्त लेजर के लिए कम अवशोषण दर होती है, जिससे बड़ी मात्रा में लेजर उत्सर्जन होता है, और क्योंकि अधिकांश लेजर का उपयोग किया जाता है ऊर्ध्वाधर में सामग्री या थोड़ी मात्रा में झुकाव के कारण, लौटने वाली लेजर लाइट आउटपुट हेड में फिर से प्रवेश करती है, और लौटने वाली रोशनी का भी हिस्सा ऊर्जा-संचारित फाइबर में युग्मित होता है, और फाइबर के साथ वापस अंदर तक प्रेषित होता है लेज़र का, जिससे लेज़र के अंदर मुख्य घटक उच्च तापमान पर बने रहते हैं।
जब लेज़र वेल्डिंग के दौरान परावर्तनशीलता बहुत अधिक हो, तो निम्नलिखित समाधान लिए जा सकते हैं:
3.1 एंटी-रिफ्लेक्शन कोटिंग का उपयोग करें या सामग्री की सतह का उपचार करें: वेल्डिंग सामग्री की सतह को एंटी-रिफ्लेक्शन कोटिंग के साथ कोटिंग करने से लेजर की परावर्तनशीलता को प्रभावी ढंग से कम किया जा सकता है। यह कोटिंग आमतौर पर कम परावर्तन वाली एक विशेष ऑप्टिकल सामग्री होती है जो लेजर ऊर्जा को वापस परावर्तित करने के बजाय अवशोषित करती है। कुछ प्रक्रियाओं में, जैसे कि वर्तमान कलेक्टर वेल्डिंग, सॉफ्ट कनेक्शन इत्यादि, सतह को उभरा भी किया जा सकता है।
3.2 वेल्डिंग कोण को समायोजित करें: वेल्डिंग कोण को समायोजित करके, लेजर बीम को वेल्डिंग सामग्री पर अधिक उपयुक्त कोण पर आपतित किया जा सकता है और प्रतिबिंब की घटना को कम किया जा सकता है। आम तौर पर, लेजर बीम को वेल्डेड की जाने वाली सामग्री की सतह पर लंबवत रूप से घटना करना प्रतिबिंब को कम करने का एक अच्छा तरीका है।
3.3 सहायक अवशोषक जोड़ना: वेल्डिंग प्रक्रिया के दौरान, वेल्ड में एक निश्चित मात्रा में सहायक अवशोषक, जैसे पाउडर या तरल, जोड़ा जाता है। ये अवशोषक लेजर ऊर्जा को अवशोषित करते हैं और परावर्तनशीलता को कम करते हैं। विशिष्ट वेल्डिंग सामग्री और अनुप्रयोग परिदृश्यों के आधार पर उपयुक्त अवशोषक का चयन किया जाना चाहिए। लिथियम बैटरी उद्योग में, इसकी संभावना नहीं है।
3.4 लेजर को संचारित करने के लिए ऑप्टिकल फाइबर का उपयोग करें: यदि संभव हो, तो परावर्तन को कम करने के लिए वेल्डिंग स्थिति में लेजर को प्रसारित करने के लिए ऑप्टिकल फाइबर का उपयोग किया जा सकता है। वेल्डिंग सामग्री की सतह के सीधे संपर्क से बचने और प्रतिबिंब की घटना को कम करने के लिए ऑप्टिकल फाइबर वेल्डिंग क्षेत्र में लेजर बीम का मार्गदर्शन कर सकते हैं।
3.5 लेजर मापदंडों को समायोजित करना: लेजर शक्ति, फोकल लंबाई और फोकल व्यास जैसे मापदंडों को समायोजित करके, लेजर ऊर्जा के वितरण को नियंत्रित किया जा सकता है और प्रतिबिंब को कम किया जा सकता है। कुछ परावर्तक सामग्रियों के लिए, लेज़र शक्ति को कम करना परावर्तन को कम करने का एक प्रभावी तरीका हो सकता है।
3.6 बीम स्प्लिटर का उपयोग करें: एक बीम स्प्लिटर लेजर ऊर्जा के हिस्से को अवशोषण उपकरण में निर्देशित कर सकता है, जिससे प्रतिबिंब की घटना कम हो जाती है। बीम विभाजन उपकरणों में आमतौर पर ऑप्टिकल घटक और अवशोषक शामिल होते हैं, और उपयुक्त घटकों का चयन करके और डिवाइस के लेआउट को समायोजित करके, कम परावर्तनशीलता प्राप्त की जा सकती है।
4. वेल्डिंग अंडरकट
लिथियम बैटरी निर्माण प्रक्रिया में, किन प्रक्रियाओं के कारण अंडरकटिंग होने की अधिक संभावना है? अंडरकटिंग क्यों होती है? आइए इसका विश्लेषण करें.
अंडरकट, आम तौर पर वेल्डिंग कच्चे माल एक दूसरे के साथ अच्छी तरह से संयुक्त नहीं होते हैं, अंतर बहुत बड़ा होता है या नाली दिखाई देती है, गहराई और चौड़ाई मूल रूप से 0.5 मिमी से अधिक होती है, कुल लंबाई वेल्ड लंबाई के 10% से अधिक होती है, या अनुरोधित लंबाई उत्पाद प्रक्रिया मानक से अधिक है।
पूरी लिथियम बैटरी निर्माण प्रक्रिया में, अंडरकटिंग होने की अधिक संभावना है, और यह आम तौर पर बेलनाकार कवर प्लेट की सीलिंग प्री-वेल्डिंग और वेल्डिंग और स्क्वायर एल्यूमीनियम शेल कवर प्लेट की सीलिंग प्री-वेल्डिंग और वेल्डिंग में वितरित की जाती है। मुख्य कारण यह है कि वेल्डिंग के लिए सीलिंग कवर प्लेट को शेल के साथ सहयोग करने की आवश्यकता होती है, सीलिंग कवर प्लेट और शेल के बीच मिलान प्रक्रिया में अत्यधिक वेल्ड अंतराल, खांचे, ढहने आदि का खतरा होता है, इसलिए यह विशेष रूप से अंडरकट्स के लिए प्रवण होता है। .
तो फिर कटौती का क्या कारण है?
यदि वेल्डिंग की गति बहुत तेज़ है, तो वेल्ड के केंद्र की ओर इशारा करने वाले छोटे छेद के पीछे की तरल धातु को पुनर्वितरित होने का समय नहीं मिलेगा, जिसके परिणामस्वरूप वेल्ड के दोनों तरफ जमना और कटाव होगा। उपरोक्त स्थिति को देखते हुए, हमें वेल्डिंग मापदंडों को अनुकूलित करने की आवश्यकता है। सीधे शब्दों में कहें तो, यह विभिन्न मापदंडों को सत्यापित करने के लिए बार-बार किए जाने वाले प्रयोग हैं, और जब तक उचित पैरामीटर नहीं मिल जाते तब तक डीओई करते रहें।
2. वेल्डिंग सामग्री के अत्यधिक वेल्ड अंतराल, खांचे, ढहने आदि से अंतराल को भरने वाली पिघली हुई धातु की मात्रा कम हो जाएगी, जिससे अंडरकट होने की अधिक संभावना होगी। यह उपकरण और कच्चे माल का प्रश्न है। क्या वेल्डिंग कच्चा माल हमारी प्रक्रिया की आने वाली सामग्री आवश्यकताओं को पूरा करता है, क्या उपकरण सटीकता आवश्यकताओं को पूरा करती है, आदि। सामान्य अभ्यास आपूर्तिकर्ताओं और उपकरण के प्रभारी लोगों को लगातार प्रताड़ित करना और पीटना है।
3. यदि लेजर वेल्डिंग के अंत में ऊर्जा बहुत तेजी से गिरती है, तो छोटा छेद ढह सकता है, जिसके परिणामस्वरूप स्थानीय अंडरकटिंग हो सकती है। शक्ति और गति का सही मिलान अंडरकट के गठन को प्रभावी ढंग से रोक सकता है। जैसा कि पुरानी कहावत है, प्रयोगों को दोहराएं, विभिन्न मापदंडों को सत्यापित करें और तब तक डीओई जारी रखें जब तक आपको सही पैरामीटर न मिल जाएं।
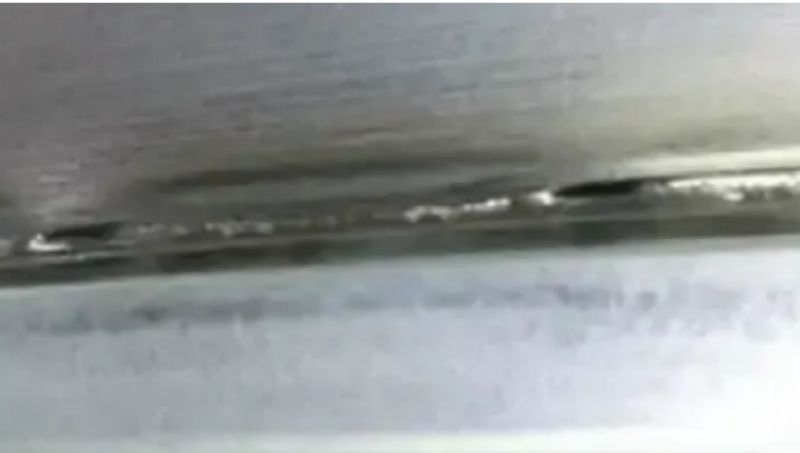
5. वेल्ड केंद्र पतन
यदि वेल्डिंग की गति धीमी है, तो पिघला हुआ पूल बड़ा और चौड़ा होगा, जिससे पिघली हुई धातु की मात्रा बढ़ जाएगी। इससे सतह के तनाव को बनाए रखना मुश्किल हो सकता है। जब पिघली हुई धातु बहुत भारी हो जाती है, तो वेल्ड का केंद्र डूब सकता है और डिप्स और गड्ढे बन सकते हैं। इस मामले में, पिघले हुए पूल के पतन को रोकने के लिए ऊर्जा घनत्व को उचित रूप से कम करने की आवश्यकता है।
एक अन्य स्थिति में, वेल्डिंग गैप बिना छिद्र किए ही ढह जाता है। यह निस्संदेह उपकरण प्रेस फिट की समस्या है।
लेजर वेल्डिंग के दौरान होने वाले दोषों और विभिन्न दोषों के कारणों की उचित समझ किसी भी असामान्य वेल्डिंग समस्या को हल करने के लिए अधिक लक्षित दृष्टिकोण की अनुमति देती है।
6. वेल्ड दरारें
निरंतर लेजर वेल्डिंग के दौरान दिखाई देने वाली दरारें मुख्य रूप से थर्मल दरारें होती हैं, जैसे क्रिस्टल दरारें और द्रवीकरण दरारें। इन दरारों का मुख्य कारण वेल्ड के पूरी तरह जमने से पहले उत्पन्न होने वाली बड़ी सिकुड़न शक्ति है।
लेजर वेल्डिंग में दरारें आने के निम्नलिखित कारण भी हैं:
1. अनुचित वेल्ड डिज़ाइन: वेल्ड की ज्यामिति और आकार का अनुचित डिज़ाइन वेल्डिंग तनाव एकाग्रता का कारण बन सकता है, जिससे दरारें पड़ सकती हैं। समाधान वेल्डिंग तनाव एकाग्रता से बचने के लिए वेल्ड डिज़ाइन को अनुकूलित करना है। आप उपयुक्त ऑफसेट वेल्ड का उपयोग कर सकते हैं, वेल्ड का आकार बदल सकते हैं, आदि।
2. वेल्डिंग मापदंडों का बेमेल: वेल्डिंग मापदंडों का अनुचित चयन, जैसे बहुत तेज वेल्डिंग गति, बहुत अधिक शक्ति, आदि, वेल्डिंग क्षेत्र में असमान तापमान परिवर्तन का कारण बन सकता है, जिसके परिणामस्वरूप बड़े वेल्डिंग तनाव और दरारें हो सकती हैं। समाधान विशिष्ट सामग्री और वेल्डिंग स्थितियों से मेल खाने के लिए वेल्डिंग मापदंडों को समायोजित करना है।
3. वेल्डिंग सतह की खराब तैयारी: वेल्डिंग से पहले वेल्डिंग सतह को ठीक से साफ करने और पूर्व-उपचार करने में विफलता, जैसे ऑक्साइड, ग्रीस आदि को हटाने से वेल्ड की गुणवत्ता और ताकत प्रभावित होगी और आसानी से दरारें पड़ सकती हैं। इसका समाधान वेल्डिंग सतह को पर्याप्त रूप से साफ करना और पूर्व-उपचार करना है ताकि यह सुनिश्चित किया जा सके कि वेल्डिंग क्षेत्र में अशुद्धियों और संदूषकों का प्रभावी ढंग से इलाज किया जा सके।
4. वेल्डिंग हीट इनपुट का अनुचित नियंत्रण: वेल्डिंग के दौरान हीट इनपुट का खराब नियंत्रण, जैसे वेल्डिंग के दौरान अत्यधिक तापमान, वेल्डिंग परत की अनुचित शीतलन दर आदि, वेल्डिंग क्षेत्र की संरचना में परिवर्तन का कारण बनेगी, जिसके परिणामस्वरूप दरारें होंगी। . इसका समाधान वेल्डिंग के दौरान तापमान और शीतलन दर को नियंत्रित करना है ताकि ज़्यादा गरम होने और तेजी से ठंडा होने से बचा जा सके।
5. अपर्याप्त तनाव राहत: वेल्डिंग के बाद अपर्याप्त तनाव राहत उपचार के परिणामस्वरूप वेल्डेड क्षेत्र में अपर्याप्त तनाव राहत होगी, जिससे आसानी से दरारें पड़ जाएंगी। इसका समाधान वेल्डिंग के बाद उचित तनाव राहत उपचार करना है, जैसे गर्मी उपचार या कंपन उपचार (मुख्य कारण)।
जहां तक लिथियम बैटरियों की निर्माण प्रक्रिया का सवाल है, किन प्रक्रियाओं में दरारें पड़ने की अधिक संभावना है?
आम तौर पर, सीलिंग वेल्डिंग के दौरान दरारें होने का खतरा होता है, जैसे कि बेलनाकार स्टील के गोले या एल्यूमीनियम के गोले की सीलिंग वेल्डिंग, चौकोर एल्यूमीनियम के गोले की सीलिंग वेल्डिंग, आदि। इसके अलावा, मॉड्यूल पैकेजिंग प्रक्रिया के दौरान, वर्तमान कलेक्टर की वेल्डिंग भी प्रवण होती है। दरार करने के लिए.
बेशक, हम इन दरारों को कम करने या खत्म करने के लिए फिलर वायर, प्रीहीटिंग या अन्य तरीकों का भी उपयोग कर सकते हैं।
पोस्ट समय: सितम्बर-01-2023